Getting ISO 13485 Certified in Memphis, Tennessee (TN)
ISO 13485:2016 is a recognized universal standard for a quality management system (QMS) in the medical device industry. The methodology includes the basis for establishing and maintaining a QMS and helps the company to show the capacity to provide medical equipment and associated services and reliably fulfill patient standards and regulatory and medical product guidelines.
The standard is developed by companies participating in one or more stages of the product life cycle, from planning and producing to assembling, installing, processing, repairing, and distributing medical devices. This is often referred to as third-party vendors offering goods such as services or raw materials.
ISO 13485’s primary purpose is to promote a structure for harmonized legislative standards for a QMS for medical equipment. This regulatory structure outlines the organization’s obligation to recognize and fulfill requirements that may involve satisfying regulatory standards as specified by each nation, sector, or discipline.
Regulatory standards are sometimes more complex than the recommendations of the ISO 13485 standard, especially in the fields of complaint handling, controlling labels, etc., and ought to be incorporated in the QMS process to include compliance evidence.
ISO 13485 is a separate standard focused primarily on the business-oriented concept of ISO 9001, with the added emphasis on particular criteria related to medical devices such as drug- and process-oriented risk identification, traceability, and sterile manufacturing. ISO 13485 certification does not mean you conform with ISO 9001.
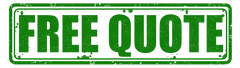
ISO Pros are here to help you get certified
Third-party analysis of the QMS of a company includes external and internal assurance of the inspection, evaluation, and regulation of the systems for customers, including creating confidence to satisfy relevant regulatory requirements. This standard is designed to aim for constant product development and consistent quality, and time and cost reduction after this standard is introduced.
Organizations participating in one and maybe more phases of a product’s life-cycle, including design and development leading to the manufacture, storage/distribution, installation, or operation of medical equipment, benefit from the experience of our technical staff in quality control. As a trusted advisor in the full audit process, we promote accountability and consistency.
Although ISO Pros in Memphis, Tennessee (TN) aims to build a safer environment, ISO 13485 promotes the elimination of unforeseen risks and enhances the handling of such hazards to achieve the optimal goals of the organization. This improvement not only improves the image of the company in the views of its clients but also provides a realistic and efficient way to demonstrate adherence to regulatory requirements
If regulatory requirements mandate omission of development and design controls, this may be seen as a confirmation for removing them from the QMS. Such regulations will have alternate solutions to be discussed in the QM framework. It’s the organization’s duty to make sure that ISO 13485 enforcement statements represent the absence of development and design controls.
Unless a requirement in Clauses 7 of the ISO 13485 standard is not valid because of the nature for the medical device on which the QMS is applied, then the company does not have to incorporate this requirement in the QMS.